The Flow of Goods Depends on the Flow of Data: How Hyperconnected Supply Chains Boost Supply Chain Efficiency and Impact Fill Rates
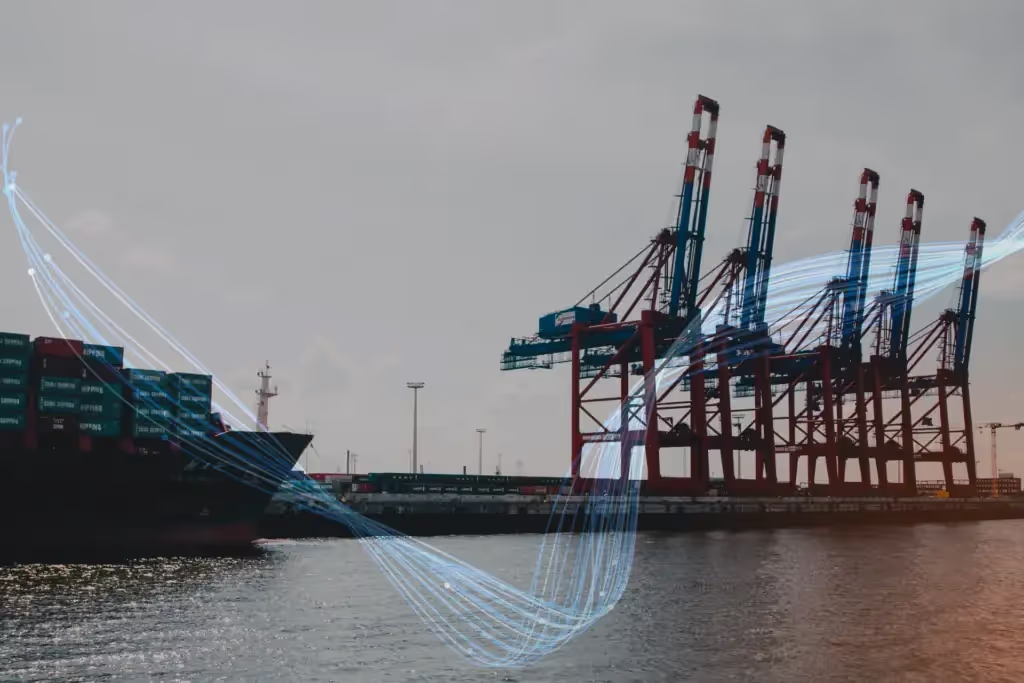
Importance behind Data when it comes to Increasing Goods
As goods are created and move through the supply chain, data should be captured at every point along the way – from raw material sourcing through the manufacturing stages to the distribution network to the end-customer, and ideally, even through the entire product lifecycle. These snippets of data, when brought together and used properly, can enable extremely powerful improvements along the supply chain, impacting how goods and services will be perceived by customers in the future. Because of today’s hyperconnected supply chains, the flow of goods is directly influenced by the flow of data – both from the source company and its customers.Because of how important supply chain efficiency is – 83% of businesses perceive resilient and efficient supply chains as crucial for the overall customer experience – business leaders’ ability to optimize fill rates, lead times, and every other aspect of their SCs will directly impact first time revenue as well as repetitive business through customer retention, and simultaneously significantly save cost on transportation, warehousing, process optimization, time savings and more. Luckily, today’s hyperconnected supply chains and the data that links them together can be used as powerful business tools, especially in the aftersales market.There is a famous saying in the machinery industry, that the first machine is sold by the sales guy and the second one is sold by the technician. Aftersales have become more relevant than ever before in today's highly competitive markets. At the same time, proactive aftersales management, meaning ensuring global parts and service availability, requires predicting the unpredictable. And doing so, requires data. From end to end, because what holds true in many dimensions is even stronger in aftersales: the flow of goods depends on the flow of data.
The Anatomy of Hyperconnected Supply Chains
In the age of hyperconnected supply chains, supply chains can no longer be thought of as a linear flow of goods or services; thinking about them as going from the manufacturer to the customer isn’t just oversimplified, but it’ll hold your business back. Instead, start to think about supply chains as complex webs with a multi-directional flow between every juncture in the web. From raw material sourcing to manufacturing to dealers, distributors, service facilities to the end-customer. And everybody depends on everyone on this website. With every single day of business, these webs get even more complex. The right mix of technology can help take complexity out of that web, however, the overwhelming amount of technology available can also add up complexity when used in the wrong mix with the wrong data.Internet of Things devices, cloud computing, and big data are all critical aspects of hyperconnected supply chains that were barely part of the conversation a decade ago. By enhancing the ability of OEMs to capture and draw insights from data within the supply chain cycle, these technologies potentially enable forward looking supply chains to serve customer needs like never before. But with these enhancements comes a very real layer of challenges, and ever-growing customer expectations.Hyperconnected supply chains carry a huge variety of advantages for everyone involved (Supplier, OEM. Dealer, Customers), including massive opportunities for topline growth through faster customer acquisition and retention with global availability of whatever is needed, as well as minimizing operational cost through seamless supply chain operations (warehousing, transport, pricing, sourcing and planning). The most important aspect of it is most probably to have the right balance between product availability and working capital needs in complex global networks. Such an imbalance costs a huge amount of money, now and in the future (also see the blog article about the Bullwhip Effect).
Implementing Data Strategies for Hyperconnected Supply Chains
However, these hyperconnected supply chains are now only as good as the data that supports them, putting pressure on OEMs to invest in the right tools, nail down airtight data processes and policies, and ensure every tool integrates into the bigger picture– internally and externally. One of the best ways to support this new architecture of supply chains today is by employing a data strategy that incorporates the needs and wishes of everyone involved along a supply chain. Whilst suppliers mainly seek data, OEMs sometimes want to get more control over their partners stock beyond the mere visibility and dealers seek more simplified workflows in order to hand out their data. This trade-off of needs and wishes must be well thought through, but once implemented there are only winners.There are platforms to allow for such give and take approaches, allowing for seamless integration, two-way data relationships, ample data storage and most importantly: a value driven operationalization of the data for the higher goal of serving customers before they know they need something – OEMs need all of these things to compete and succeed in today’s business environment.While it may seem like a huge effort to push every stakeholder along a supply chain on a new technical infrastructure, the reality is quite the opposite. Designed with legacy systems in mind and hesitance from multiple players to change their way of working, solutions like the ClearOps aftersales platform help to integrate all relevant systems that are already there without changing anything but leveraging their data in the most sophisticated and modern way. That way, companies can centralize even the most disparate processes and systems, enabling new levels of hyperconnectivity and supply chain efficiency.
Understanding the Relationship Between Data Flow and Supply Chain Efficiency
The supply chain doesn’t stop when goods or services reach a customer. In fact, the true data play starts way earlier, and will never end. Once goods have reached the customer, the digital bridge between suppliers, OEMs, dealers and end-customers must truly start working though. Customers will repeatedly need something, whether its sole support and information, a wear part exchange, a foreseeable service or in the worst case: a repair for a still standing machine.Customers are willing to pay money to satisfy their needs, but in today's world, their needs must be satisfied immediately. Foreseeing and exceeding customer expectations in aftersales, as an OEM for instance, requires an interesting mix of technologies. IoT data must be matched with service profiles, upcoming services must be matched with technician skills and availability, future forecasting's must be matched with dealer stock, sales must be put in a relation with the assets in the field, rather than the warehouses that parts were sold to. There is a bunch of data that must be gathered, matched and leveraged.Then, through the hyperconnected supply chain web, they can pair those insights with production plans, dealer inventories servicing nearby machines, technicians and every other stakeholder involved and put a plan of action in place to ensure there is no product downtime for the customer. At the end of the day, this approach will meet and even exceed customer expectations and directly boost their level of satisfaction with the OEM.
The Role of Data in OEM-Dealer Partnerships:
The collaboration between OEMs and dealers is nothing new; the two have always had to work together to ensure end users get the support and replacement parts they need. With the use of Retail Inventory Management (RIM) programs, OEMS and dealers can collaborate and communicate with newfound ease. Ushering in an era of advanced inventory management, RIMs provide a stronger-than-ever link between OEMs and dealers, improving fill rates, providing a proactive service model, and cutting down on business waste.Advanced RIM solutions go beyond mere end-to-end inventory management though, they carry lightweight CRM capabilities to match future asset requirements with part requirements with service requirements to really display the full picture of aftersales and happy customers. Again, it’s not about having only the right parts, it’s about ensuring global machine uptime.Although the wide array of new tools within a hyperconnected supply chain can feel overwhelming at first, they provide the road map to achieving optimized supply chain efficiency. Most OEMs weren’t set up to revolve around data, but every day, the power that data has in the industry becomes clearer and more pronounced. And there has never been a better time to delve into the world of data for a world of seamlessly flowing goods.
Enhancing Fill Rates with Hyperconnectivity
OEM or not, managing inventory is a business challenge that has been around forever. Not only is it costly to store excess inventory, but if it’s not sold, the associated business losses impact the bottom line. On the other hand, if demand depletes inventory levels, customer attrition will rise, and future opportunities can be missed. When OEM customers need a replacement part or machine servicing, they need it promptly; waiting for OEMs or dealers to manufacture or source those parts isn’t always an option.Fill rates are and have always been one of the biggest challenges for the OEM ecosystem, but inventory management was brought to the forefront when overextended supply chains led to product shortages post-Covid. For electric automaker Tesla, the use of technology in a hyperconnected supply chain helped the company navigate the global chip shortage and come out ahead of other industry leaders. When automakers around the world reduced their forecasts for chips because of lockdown measures, Tesla used growth data and its hyperconnected supply chain to inform the decision to maintain inventory levels.Thus, when things started returning to normal and other OEMs scrambled to get the parts they needed, Tesla already had the inflow of crucial vehicle components, allowing them to meet product demands and secure brand loyalty worldwide. It’s impossible to predict events like a pandemic, but with reliable data hubs, OEMs can drown out the noise, figure out what their customers need, and deliver on their promises time and time again.
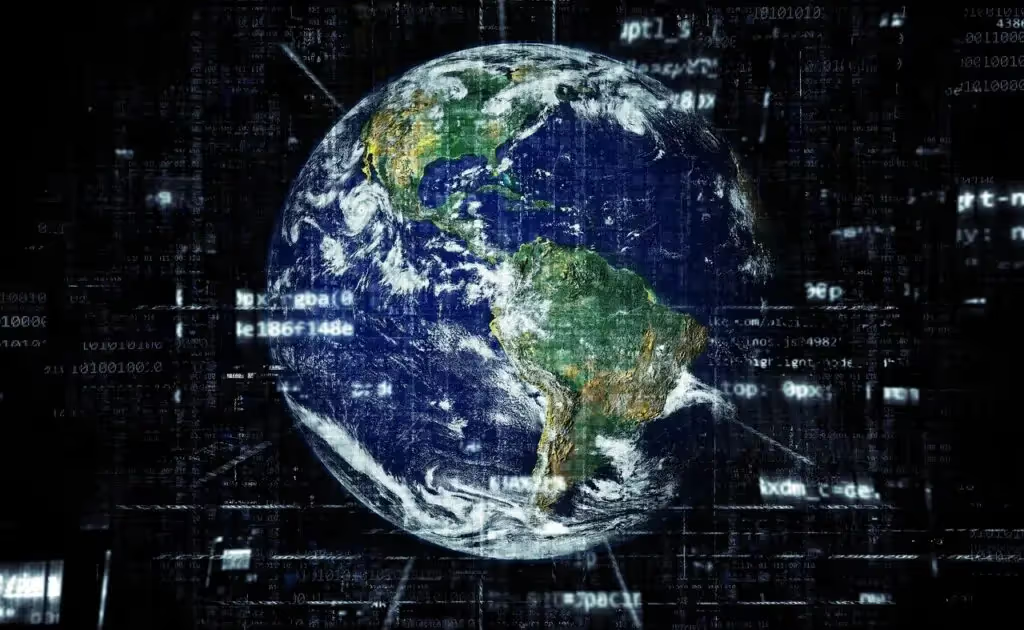
Overcoming Challenges in Hyperconnected Supply Chains
Hyperconnected supply chains are fundamentally changing the way OEMs operate. Standing at the helm of such transformation doesn’t come without challenges, but with the right understanding of these challenges, they become much more manageable. As OEMs and those involved in their supply chain web adapt and evolve, some of the biggest challenges they’ll face are:
Resistance across the stakeholder network
As mentioned above, Suppliers, dealers or even end-customers might be hesitant to share data. It’s important to find out what they like and seek to get their data as an OEM. Whilst suppliers usually seek visibility for better planning, OEMs seek control over parts related processes and dealers seek relief from the burden of operating their ERP system, several different order, warranty or service systems from all their OEMs and end-customers want guarantee for machine uptime. The right mix of give and takes must be defined.
Existing infrastructure
“We have always worked like that” is a common sentence whenever you talk to such people. It’s important to make small iterative steps towards achieving end-to-end supply chain optimization, and not to overwhelm an entire network with new systems repeatedly. Working with what’s there but revolutionizing the way of working through slightly adjusted workflows and basing decisions based upon data rather than a gut feeling is a good first step.
Data Security Issues
As more cloud-based platforms are added to the OEM ecosystem, more data security vulnerabilities are exposed. It makes sense – more systems mean more access points for hackers and more opportunities for data to be corrupted. While data security issues are a cause for concern, they are by no means a reason to avoid hyperconnected supply chains.With the help of aftersales solutions, like the one ClearOps offers, creating a centralized data hub and aftersales platform is more accessible than ever. These platforms boost data security, ensure communication among business systems, and use data to inform business decisions.
Interoperability in the supply chain network
Data is not equal. It’s important to understand that every stakeholder usually works with different types of data, from a format, naming convention and workflow perspective. It’s important to understand and define the right data to look at, and the right format to analyze with. You cannot force everyone to transform their data towards a unified approach, but you can build a solution that can digest any kind of input, transform it to the structure needed and then start analyzing. Starting to analyze without taking care of the first two steps causes huge pains for everyone involved and doesn’t yield any results that make sense.
Technology Investment Costs
Investing in advanced solutions and cutting-edge technologies comes with a long list of costs. The price of the software itself as well as integration costs, training costs, and process adjustment costs are prohibitive for some OEMs. If cost is standing in the way of automating supply chain operations with data integration, start small – the whole ecosystem doesn’t have to be implemented overnight. Trust us, the advantages of cloud-based supply chain management will outweigh the investment costs in the long run.
Aftermarket Service Optimization Starts with Hyperconnectivity
Truthfully, investing in a hyperconnected supply chain is a choice, but it’s a choice with a right and a wrong answer. OEMs have seen what happens when unanticipated events throw off all business projections and cripple supply chains. Now is the time to act and prevent the fallout the industry witnessed in the last couple of years.By thinking of supply chains as a web and using technology to seamlessly connect all points on the web, OEMs will be able to make data-driven decisions in an instant. The flow of data impacts the flow of goods in a profound way, but with hyperconnected cloud-based platforms, that data can enable a proactive service model, lead to advanced inventory management, and tailor each customer’s experience to their needs.Will there be challenges along the way? Of course. However, the challenges that come with complacency in the current state of linear supply chains will be much more detrimental to OEMs than the challenges of moving forward and architecting a new service delivery model with technology.
FAQs
How have supply chains changed in recent years?Supply chains are moving from a linear flow of goods to hyperconnected webs. They must process and assess data from every point within the supply chain cycle and use that data to inform improvements. For OEMs, understanding and adapting to this hyperconnected supply chain architecture is crucial for optimizing efficiency, improving customer satisfaction, and driving business growth.How does hyperconnectivity enhance the customer experience within supply chains?Hyperconnected supply chains leverage real-time data collected by IoT-enabled devices to offer proactive service models, improve fill rates, and personalize customer experiences.What are the main challenges associated with implementing a hyperconnected supply chain?Implementing a hyperconnected supply chain comes with several challenges, including data security issues, interoperability concerns in the IoT space, and technology investment costs.How can OEMs effectively address resistance to sharing data across their supply chain network?OEMs can address resistance to data sharing by understanding stakeholders’ needs and fostering transparent, mutually beneficial partnerships.What are the potential risks and costs associated with investing in advanced technology solutions?Investing in hyperconnected supply chain technology entails initial costs for software acquisition, integration, and training, along with potential disruptions to existing workflows. Despite these challenges, the long-term benefits outweigh the investment.How do hyperconnected supply chains enable proactive service and advanced inventory management?Hyperconnected supply chains use data insights to enable proactive service models and advanced inventory management. Challenges include data security, interoperability issues, and the need for comprehensive training. However, embracing technology advancements can enhance service delivery and competitiveness.Supply chains are moving from a linear flow of goods to hyperconnected webs. They must process and assess data from every point within the supply chain cycle and use that data to inform improvements. For OEMs, understanding and adapting to this hyperconnected supply chain architecture is crucial for optimizing efficiency, improving customer satisfaction, and driving business growth.Hyperconnected supply chains leverage real-time data collected by IoT-enabled devices to offer proactive service models, improve fill rates, and personalize customer experiences.Implementing a hyperconnected supply chain comes with several challenges, including data security issues, interoperability concerns in the IoT space, and technology investment costs.OEMs can address resistance to data sharing by understanding stakeholders’ needs and fostering transparent, mutually beneficial partnerships.Investing in hyperconnected supply chain technology entails initial costs for software acquisition, integration, and training, along with potential disruptions to existing workflows. Despite these challenges, the long-term benefits outweigh the investment.Hyperconnected supply chains use data insights to enable proactive service models and advanced inventory management. Challenges include data security, interoperability issues, and the need for comprehensive training. However, embracing technology advancements can enhance service delivery and competitiveness.
We want you to succeed!
Maximize your success in a decentralized dealer network with our comprehensive guide.
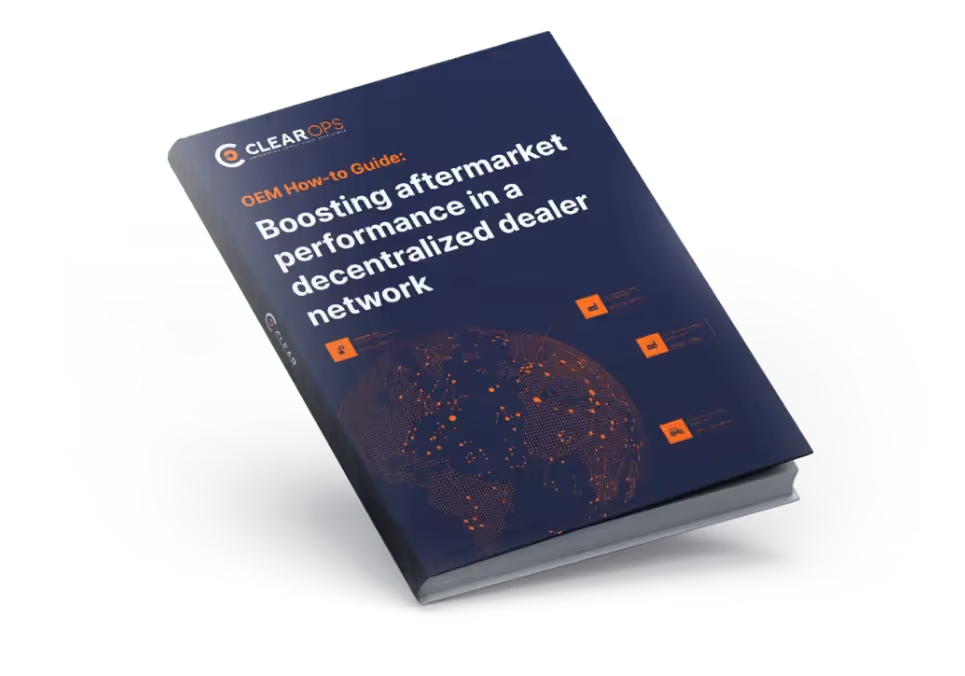
Book your free demo!
Get in contact with us today - see your Aftersales Success tomorrow.
ClearOps is an aftersales platform that enables collaboration between manufacturers, dealers and end customers.
We are already trusted by the world's leading manufacturers and over 8000 associated dealers.