Real Cost of Machine Downtime [Free Whitepaper]
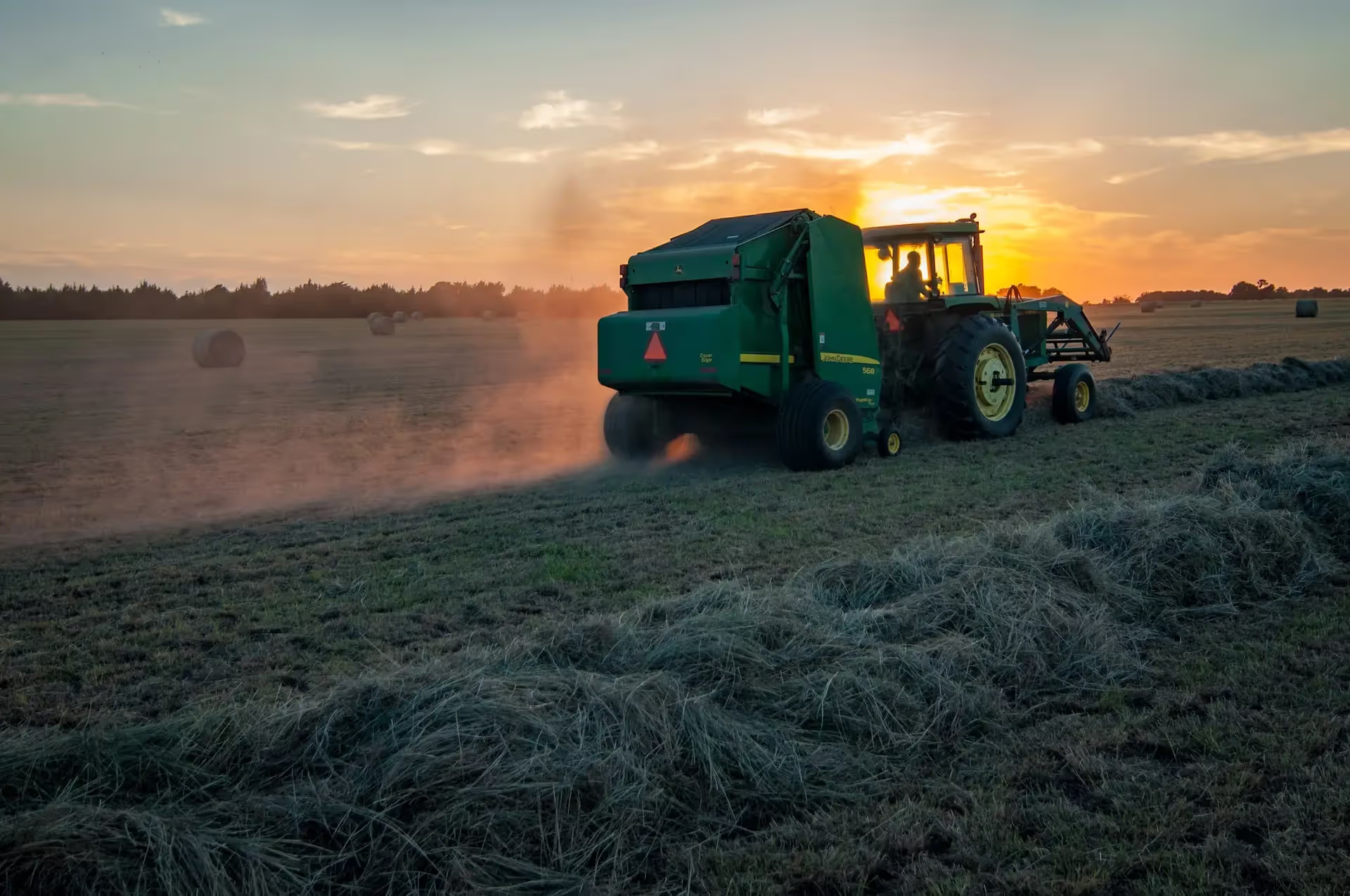
Refrigerators, drilling machines, automobiles, trucks, excavators, harvesting machinery, and airplanes—what do all of these machines have in common?Firstly, they are most likely pricey, with some being more expensive than others. Secondly, they’re not flawless—they’re bound to breakdown at some point.The good news for manufacturers is that customers don’t expect machines to be flawless. However, they do expect their service experience to be flawless in the event that something goes wrong—especially when the consequences of machine breakdown are so severe.Whether it’s empty shelves in a supermarket when trucks break down, construction sites coming to a halt due to a malfunctioning excavator, or a missed harvesting season due to broken down harvesting machinery—machine breakdown causes far-reaching issues across industries.As an OEM, you may not be as responsible for repairs and maintenance as your dealers—but you're responsible for satisfying your customers' needs. It's not about building a perfect machine, it's about delivering a perfect customer experience.In our free whitepaper you will find out more about the costs of failing to do so.
Download The Free Whitepaper "The Real Cost of Machine Downtime"
In the whitepaper, you’ll learn:
- What machine breakdown refers to
- 7 main causes of machine breakdowns in agriculture, construction machinery, and material handling
- The shocking real cost of machine downtime in each of the three industries
- Most importantly: The real cost of machine breakdowns for OEMs and how to prevent it!
We hope you enjoy our free whitepaper about "The Real Cost of Machine Downtime"! We appreciate your interest and we’re always happy to discuss aftersales topics. Feel free to contact us.
We want you to succeed!
Maximize your success in a decentralized dealer network with our comprehensive guide.
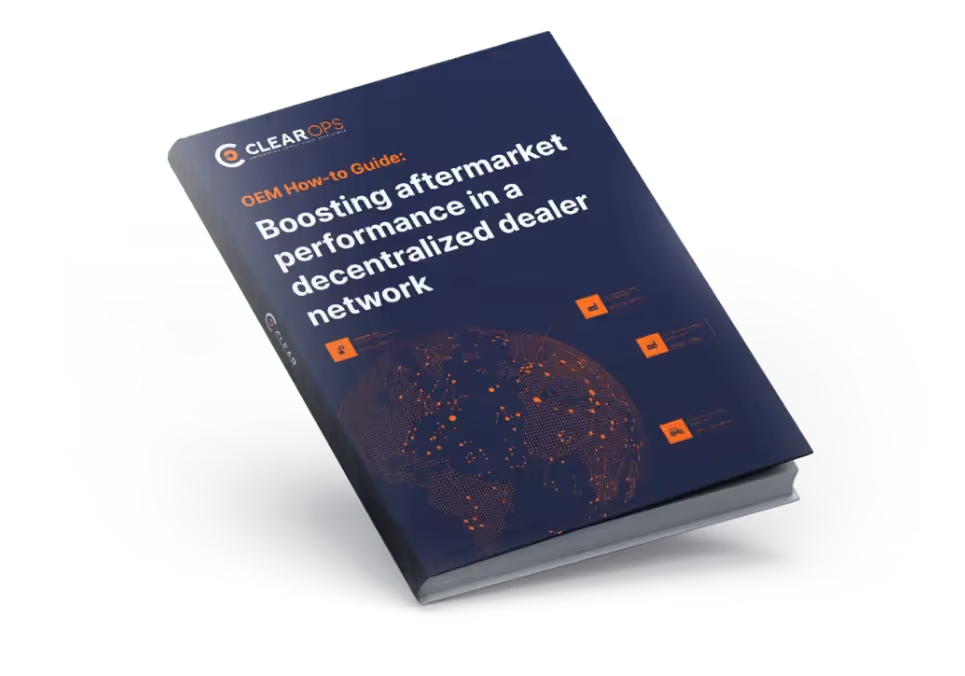
Book your free demo!
Get in contact with us today - see your Aftersales Success tomorrow.
ClearOps is an aftersales platform that enables collaboration between manufacturers, dealers and end customers.
We are already trusted by the world's leading manufacturers and over 8000 associated dealers.